澤藤電機鰍ヘ、大型自動車の電装品、発電機などに多くの実績を持つメーカー。環境に対する取り組みでは,すでに1997年にISO14001を取得している。
今回、同社の製造拠点である新田工場の1ラインでセミドライ化を実現した。独白の工夫を多数盛り込んだこの取り組みを紹介する。 |
きっかけは、「現場」の体験から |
今回のセミドライ化を推進した太田一成氏は,生産本部生産技術部の所属。いつもはラインの改善,効率化を指導する立場にある。2年ほど前,生産台数の増加に対応するため,1か月間生産ラインの応援に駆けつけた。実際にラインに入って使う立場になってみると、飛び散る切削油の問題が大いに気にかかったという。応援の期間が終わるのを待って「どうしてもドライ切削をやってみたい」と上司に相談,社として検討が開始された。
セミドライシステムには,植物性油をミスト状に供給するシステム(ブルーベ最少潤滑システム,フジBC技研製)を採用,同社技術者との共同の取り組みにより,2年弱をかけて実用化にこぎ着けた。
今回セミドライ加工を適用したのは,発電機のアウターロータのヨーク(外枠)とハブ(中心になる鍛造品)の削り。材料はS35C相当の冷間鍛造品,熱間鍛造品。
ラインの構成はこうだ。
・ロータの中心となるハブの外径旋削→
・同じくハブの外径旋削→
・ハブヘの穴加工→
・プレス成形されたヨークとハブとのかしめ→
・ハブ内径のテーパの旋削加工(逆テーパ)→
・ハブへのタップ加工→
・ハブ内径へのキー溝のブローチ加工
の7工程である。
このうち,切削加工の6工程すべてにセミドライ加工システムが適用された。切削時間は1台約1分程度。2人の作業者で対応し,1日に300〜400個の製品を加工する。
工程のうち,外径旋削は比較的困難なくセミドライ化が行なえた。また,穴あけ,タップとも,深さが4mm程度と浅いため,これも容易にセミドライ化への置き換えがなされた。 問題があったのがハブの内径旋削。これは,逆テーパになっている内径を加工するため,切屑はけの悪さが問題となった。そのため,加工プログラムでバイトをインチングするようにして切屑を細かくするとともに,それまで外部給油方式であったものを,ミストホール付きバイトに変更,内部給油方式システム(ミストの粒子径2μm以下として,ミストの搬送効率を向上させた方式)を適用して,加工部にオイルミストが確実に届くようにすることで問題を解決した。
ラインの最終工程であるブローチ加工にも問題があった。ブローチ加工の場合,ミスト加工で切削性には問題はなかったものの,やはり切屑の処理に悩まされた。刃面に堆積する切屑をうまく取り除かなければならない。そのためにワイヤブラシなどを使用してみたが,すぐに減ってしまい,実用にはならないことが判明した。太甲氏らは,市販されている薄い厚み調整用の金属板を切って何枚か重ねたものを用意し,そこを刃が通って切屑を除去する独自の機構を考案,試行錯誤の結果,満足できる独自の切屑除去機構を完成させた。
|
工具寿命延長も実現 |
セミドライ化の成功で,作業環境は見違えて良好になった。さらに,従来このラインで年に2回行なわれていた切削油の交換が不要になった。また,公差が厳しい部分が何か所かあり,そこでは定期的な補正が必要であったが,セミドライ化により,次回の補正までの期間を2倍程度に伸ばすことが可能となるなど,切削油そのもののコスト、メンテナンスコスト,産廃処理費用などが削減される効果が出た。
さらに,工程の一部の加工では,従来に比べ,工具寿命が1・5〜2倍に延びることが確認できている。現在この工程では、ヨーク(外枠)がプレス加工時の油が付いたまま導入されているため,ブローチ加工の後,洗浄工程を経てヨークヘの磁石の貼り付けが行なわれている。太田氏らは,今後このヨークの油を事前に取る(油を付けない)ことにより,磁石貼り付けの工程までつながった一つの工程として組み上げていくことを考えている。
さらに,このラインにおけるセミドライ化の成功を受けて,現在,アルミのハウジング(ディーゼルエンジン用スタータ)加工ラインへのセミドライ加工導入の検討に入っている。
将来に向けて環境への対応は避けては通れない,との認識から,加工におけるドライ化,セミドライ化は,各所で試みられているが,それぞれが難しさを抱えている。それは,加工物,工具,工作機槻,加工条件,要求精度など,すべてがあまりにも多様なため,単一の技術の適用が難しいことにある。それぞれの現場で独自の対応,独自の工夫が必要とされる。「お手本」がない自社の"環境対応技術"を完成するには地道な努力が必要とされる。しかしそれを完成させることによる波及効果は少なくない。これからの"環境対応技術"では,作業環境を改善することは当然のこととして,澤藤電機の例のように,さまざまなコスト削減を実現する相乗効果も含んだ技術開発が期待される。 (小山宏 機械と工具)
|
【澤藤電機株式会社】
1908年,澤藤電機工業所として創業。34年,現在の社名に改称。36年,自動車用電装品(スタータ,ゼネレータなど)の製造販売を開始。49年,東証、大証一部に上場。65年,発動発電機用ゼネレータの製造販売を開始。76年.本社を練馬区に移転新田工場の操業開始。99年,リターダの製造販売を開始。2000年,オーストリアに子会社,2001年.イギリスに子会社を設立。
資本金10億8,500万円。2002年度の売り上げ262億7,900万円のうち、発電機が54%,電装品が35%を占める。
<主な製品>
○電装品 ディーゼルトラックなど向けの,スタータ,オルタネータ,DCモータ,リターダなど。
○電子製品 ESスタート,FFシフトなど。
○汎用発電機 電圧の品質を向上させたインバータ発電機が主流(0.3kVAから20kVA)。
○車搭載用冷蔵庫 キャンピングカー用,トラック用,クルーザー用など。
本 社:東京都練馬区豊玉北6−15−14
Tel.(03)5999−3355
新田工場:群馬県新田郡新田町早川3
Tel.(0276)56−7111
製造の拠点である新田工場の敷地面積は15万9,856m2,全社員約840名中,約760名が働く。
URL http://www.sawafuji.co.jp |
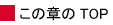 |
本原稿は著者及び初出誌出版社の許可を得て掲載しています。
Copyright esPLANET2004 |